Approximate rubber tires diverted from the landfill by Malarkey by incorporating upcycled rubber into our shingles.
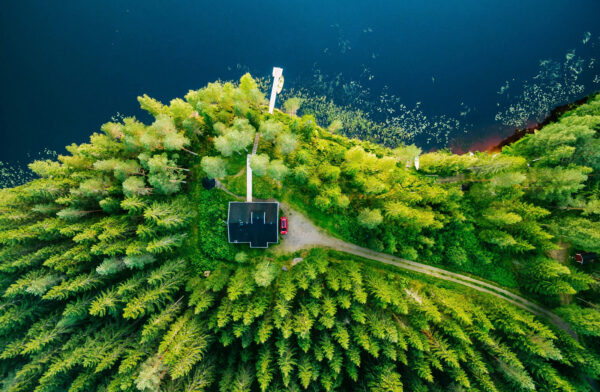
At Malarkey, we invented the cleaner, longer-lasting shingle technology known as polymer modified (rubberized) asphalt. We pioneered the use of upcycled rubber in shingles. We pioneered the use of upcycled plastic in shingles. And we launched the industry’s first smog-reducing shingle.
Approximate rubber tires diverted from the landfill by Malarkey by incorporating upcycled rubber into our shingles.
Approximate plastic bags diverted from the landfill by Malarkey by incorporating upcycled plastic into our shingles.
Approximate trees ‘planted’ by Malarkey to help clean the air by adding smog-reducing granules atop our shingles.
Approximately 5 rubber tires diverted from the landfill per roof of Malarkey shingles.
Approximately 3,200 plastic bags diverted from the landfill per roof of Malarkey shingles.
Approximately 2 trees ‘planted’ to help clean the air of pollutants per roof of Malarkey shingles.
If there’s a better, more sustainable way to make a roofing shingle, we intend to find it.
Our NEX® Polymer Modified (Rubberized) Asphalt formulation enhances shingles’ durability, impact resistance, and granule adhesion, so shingles last longer – the very definition of sustainable.
Our NEX® Polymer Modified (Rubberized) Asphalt is a cleaner shingle-making technology, resulting in much less emissions than the oxidized asphalt method of making standard shingles.
Malarkey is also GreenCircle® certified for Recycled Product Content and Waste Diversion from Landfill at all its manufacturing facilities.
Portland, OR Certificate
Oklahoma City, OK Certificate
South Gate, CA Certificate
By integrating smog-reducing granules atop our shingles, Malarkey helps clean the air of emission-based pollutants.
UL-Certified Environmental Product Declaration PDF files available.
“Granted, it’s just one roof, but if everyone starts choosing a shingle that reduces landfill waste and fights air pollution, who knows what the end result will be.”
– James Martinez, Homeowner
By incorporating recycled materials into our shingles, Malarkey helps reduce landfill waste. Thanks to our continued relationship with the Department of Resources Recycling and Recovery (CalRecycle), we have been able to incorporate polymers from upcycled tires to improve shingle durability, while reducing landfill waste. In the 11th cycle of the Tire Incentive Program Grant, Malarkey diverted 83,333 tires.
We also incorporate single-use and consumer-recycled plastics into our shingles, which diverts waste plastics from our landfills and oceans and gives the shingles a longer lifespan.
Solar paneled roofs require shingles that can handle the extra burden, not only of the panels, but also the installation process, which can cause major shingle damage and granule loss.
Our NEX® Polymer Modified (Rubberized) Asphalt shingles deliver up to 30% greater strength and 65% greater granule adhesion than the industry standard for increased strength, durability, and granule retention.
Malarkey is a proud member of the United States Green Building Council® (USGBC) and actively participates in transforming how our buildings are designed, constructed and operated through LEED, the world’s most widely used green building system. To achieve LEED certification, a project earns points by adhering to prerequisites and credits that address carbon, energy, water, waste, transportation, materials, health and indoor environmental quality.