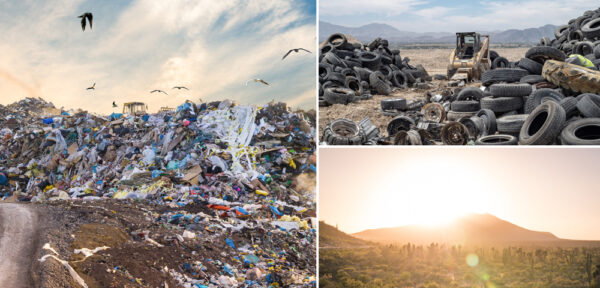
How Upcycling Improves Roofing Shingles
The core motivation for Malarkey's focus on innovation is to always to build a better roofing shingle. During this research, we also found opportunities to become a more sustainable manufacturer. The result is NEX® polymer modified asphalt, made with polymers from upcycled materials.Engineered for Performance
Leading Malarkey’s asphalt innovations since 1976, has been researching and innovating on the use of SBS polymers in roofing products to address the problem performing oxidized asphalt roofing shingles. In a shingle and on a roof, oxidized asphalt continues to oxidize – or “bake” – under exposure to heat and UV light. While granules help protect the asphalt from these elements, as the asphalt expands and contracts over time, granules become loose and fall off the shingle, thus exposing more asphalt to age prematurely. Then, after only a few years after installation, a roof suddenly appears and protects as poorly as if it had been up for decades.
Malarkey’s research and development team identified additional, specialized polymers which can be utilized in the asphalt to improve flexibility without sacrificing other attributes. Their findings then yielded a specific formula for the asphalt’s modification. This blend became the popular Flexor™ Styrene-Butadiene-Styrene (SBS) asphalt. Today, new technologies help to refine the physical characteristics desired for quality shingle performance, while also doing so with sustainability in mind.
The Problem of Plastics
At Malarkey, we recognize the value and quality of life that the verdant, open spaces provide for us. As a family company based in Oregon, Malarkey Roofing Products is especially focused on maintaining the quality of our business and environment for future generations.
We recognize the problem with single-use plastics and rubber dominating our waste stream and littering our planet. Single-use plastics and rubber are among the primary materials found in landfills (and oceans) across the world.
Reported in the peer-reviewed journal Science Advances, a recent study has found that, 'of the 8.3 billion metric tons that has been produced, 6.3 billion metric tons has become plastic waste. Of that, only nine percent has been recycled.'
While the scale of the plastic problem can be daunting, it also presents an opportunity. Through our research, Malarkey has learned that certain plastics contain valuable polymers for roofing shingles, as well as how to extract them from waste material and upcycle them into our high-performance, polymer modified asphalt.
The Solution
Whereas recycling is the process of turning waste into a reusable material, upcycling is a specific form of recycling that turns waste into a material or product that is of a higher quality. Modifying the asphalt with upcycled polymers improves the roofing shingle’s durability and performance for a longer period. Since synthetic polymers available for the asphalt modification are diverse in construction and characteristics, many of the most valuable polymers for roofing shingles can be found in upcycled materials like plastics and rubber. Malarkey adds polymers too, among other things, elevate the softening point of the asphalt, making it more flexible and resistant to UV degradation. This improvement also extends the roofing shingle’s durability and performance in a variety of conditions, such as cold weather installation.
In each manufacturing facility, Malarkey uses upcycled materials for NEX® polymer modified asphalt is in all Malarkey roofing shingles. At this scale of production, the reduction of environmental impact is substantial. For every ton of recycled plastic used, 4 barrels of oil and 7.4 cubic yards of landfill space are saved. Additionally, for every pound of recycled tire rubber used, one pound of carbon dioxide is prevented from being released into the atmosphere. This means Malarkey is building durable, performance driven roofing products with limited impact on natural resources.
For the homeowner, with an average-sized roof of roughly 3,000 square feet (30 roofing squares) with NEX® shingles, the reclaimed quality material equates to roughly 5.5 rubber tires and 3,200 plastic bags.
Furthermore, at the end of their service lives, asphalt roofing shingles themselves can be ground up and repurposed into material for road paving. The reduction in environmental impact is dramatic, but the focus has always been to create a better roofing shingle.
Durable Roofing Shingles Avoid Landfills
By increasing the performance and longevity of our roofing products, they are diverted from premature entry to the waste stream that occurs with oxidized asphalt roofing products. For instance, flexibility of NEX® polymer modified asphalt offer exceptional flexibility. This flexibility, plus the use of SEBS seal-down adhesive, prevents shingle blow off in high winds, making the shingle more durable and less likely to create waste. As compared to traditional oxidized asphalt, NEX® products provide a longer life cycle. The polymers in NEX® also fortify the shingle with Class 3 impact resistance and extreme weather. Roofing materials rated for Class 3 impact resistance withstand impacts from simulated hail stones up to 1 ¾” in diameter, lessening the impact of tear-offs and waste.
In closing, Malarkey Roofing Products manufactures performance-driven shingles that withstand extreme weather conditions with an extended service life on the roof. Today, we’re doing so with sustainability in mind, using polymers from upcycled materials. Simply put, it is the NEX® step in our continuous innovation to manufacture premium quality roofing shingles. It is the same goal we’ve had since 1956, and the same goal we’ll pursue tomorrow.